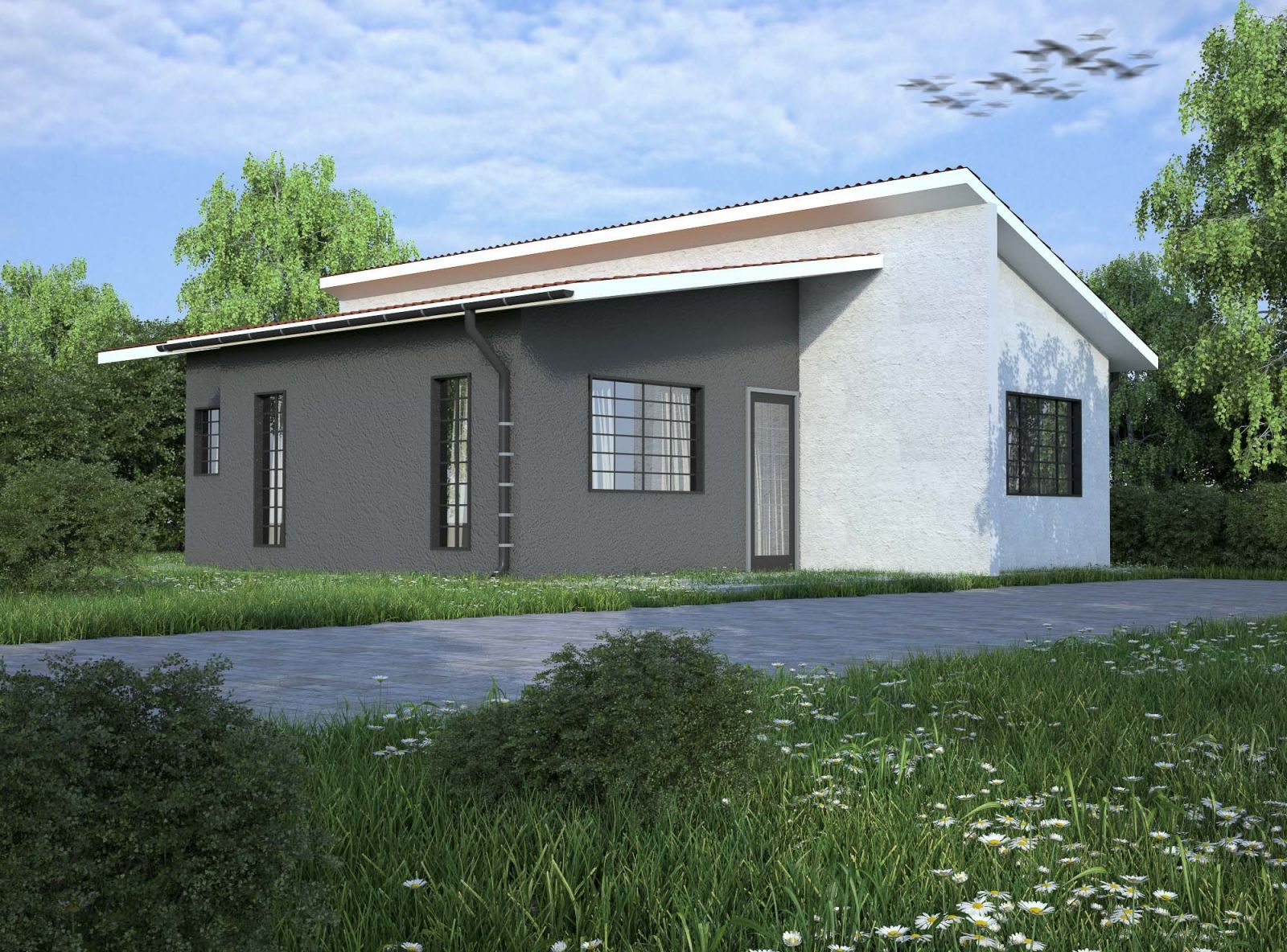
The demand for prefabricated items for houses and road construction, like blocks and culverts, has increased tremendously with the growth of Kisumu’s real estate sector. This increase has been the gas fueling Ms Christine Jackino’s firm, Building Construction Concepts Ltd.
Her eight-year-old company, more famous in Kisumu as B-Concepts, is one of those that have seen business boom in the past few years.
They sell a range of building and finishing materials, including wall blocks at Sh200, ventilators at Sh50, balcony spindles at Sh300, and louvre blocks at Sh80. They also sell flooring slabs, tiles, pillar heads and paving blocs.
At the firm’s workshop, preparation of prefab materials begins with mixing of concrete, which is then casted on steel containers that moulds it into shapes depending on their use. After over 14 hours, the concrete is removed and cured in a controlled chamber to make it strong and long lasting.
“The concrete is made form from ballast, dust and cement in a ratio of 4:3:3. We normally use amounts that our concrete batch mixer machine can hold, which is 400 kilogrammes of ballast, 300 kilogrammes of dust, six 50kg bags of cement and water.
SPECIAL BLOCK
The machine mixes it thoroughly for one minute before hardener liquid is added,” explains Ms Jakino. But for wall blocks, there is a special block making machine that compresses the concrete before it is left to dry.
With prefabrication, one avoids transporting so many skilled workers to the construction site as prefab materials can be made at a location where skilled labour is available, while reducing congestion at the building site, which wastes time.
Another advantage is that one avoids restricting conditions such as a lack of power, lack of water, exposure to harsh weather or a hazardous environment at the site.
However, care must be taken when transporting and lifting the prefabs into position as they will usually be larger, more fragile and more difficult to handle than the materials and components of which they are made.
“To make it a one-stop-shop for clients, we also have a timber machine that processes wooden doors, kitchen cabinets and other carpentry works for a house,” said Ms Jakino.
Her enterprise, which can now supply hundreds of thousands of building blocks in a week, or 20 culverts in a single day, took a long time to reach here since inception in 2007. It was Patrick Jakino, Christine’s husband and a civil engineer, who came up with the idea of starting a construction project.
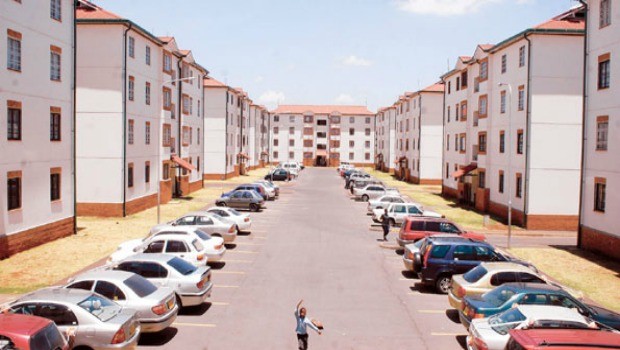
SAW A VOID
“My husband used to travel across the country and to Sudan for construction projects. He saw a void in the prefabs sector and asked me to support him in starting the project,” said Ms Jakino.
They registered a company and leased a plot along the Kisumu-Kakamega highway. At the time, there was only one Indian firm in the sector in Kisumu, and it was difficult convincing locals that their peers could produce equally good materials.
But they only had one mould which could shape fencing poles and they borrowed a second one from a friend. Considering the concrete had to remain in the mould overnight to avoid breaking, they were forced to make additional blocks manually and people did not like them as they were not finely lined.
They then had to use up their Sh1.3 million capital to purchase the basic equipment they needed to run the business.
“After using up the capital, we were left with none to purchase raw materials. We got disadvantaged when we realised most people needed ready-made items and not by order,” said the managing director.
They had been working for a full year on small scale items before they won over clients with larger orders. “A client had a big contract. He gave a deposit of 40,000 for paving floods road culverts and wall copings. We bought materials worth the amount from one hardware shop and asked them to give us additional materials on credit,” she explained.
They managed to deliver the items, worth close to Sh1 million, which enabled their business to produce items in advance and gain continuity.
In 2013, they topped up the proceeds from the business and bought bigger machines to meet the customer demand.
“We supplied some of the culverts used around the Kisumu International Airport and it’s a good feeling, considering how far we came from,” said Ms Jakino.
The company has since opened another branch in Kisii.
PREFABS TRUSTED SINCE THE 1800S
Prefabricated houses were widely constructed in the 20th century, such as in the United Kingdom to replace houses bombed during World War II. Assembling sections in factories saved time on-site and reduced cost. In 19th century Australia, a large number of prefabricated houses were imported from the United Kingdom, while the Sinhalese kings of ancient Sri Lanka used prefabricated buildings technology to erect giant structures, which date back as far as 2000 years.