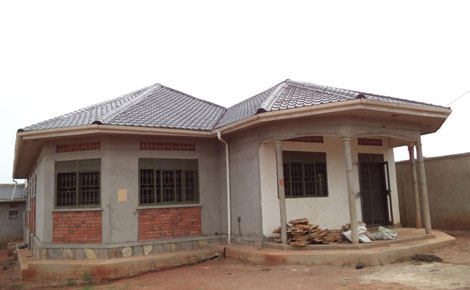
Depending on the design, assembling prefabricated houses can take between a few weeks to six months on average with minimal material losses since the panels are prepared in a factory. Industry estimates put the price of these houses at between Sh3 million for a three-bedroom house and Sh8 million for a five-bedroom house – an estimated 30 per cent saving over the brick-and-mortar variety. Compared to brick-and-mortar houses, prefabricated houses, therefore, bring the dual benefits of cost-effectiveness and time efficiency – key considerations for many potential home owners.
Interlocking blocks
More developers in Kenya are also opting for interlocking blocks, which are made of compressed soil, cement and sand or quarry dust.
The blocks are designed like two adjoining pieces of a jigsaw puzzle with each block having a projection at one end and a depression at the other so that they always align perfectly. Compared to brick-and-mortar, interlocking blocks are gaining popularity in Kenya, largely because of their benefits. Besides the material needed to produce them being readily available, interlocking blocks can be laid and aligned with simplicity, reducing the cost of labour and time needed to erect a structure. Additionally, this technique is more durable and environmentally-friendly compared to timber.
Read:Â Top 10 Politicians With Most Expensive Homes and Houses In Kenya 2017
International Green Structures
Potential homeowners can also consider International Green Structures (IGS) technology, which uses agricultural residue such as rice and wheat, which are compressed into Compressed Agricultural Fibre (CAF) panels. The CAF panels are then joined to pre-engineered framing system to make strong and durable IGS structures.
This technology has been made locally available by an American firm, IGS, which earlier this year announced it was putting up a Sh1.3 billion panel-making factory in Thika, with a capacity to build 12,000 housing units per year. Compared to brick-and-mortar, this innovative building technology brings forth a sturdy structure made of energy-efficient panels resistant to fire, water, moulds and pests.
Further, a key advantage of this technique is the speed with which an IGS structure can be put up. For instance, according to IGS Kenya, a two-bedroom, one-bathroom 46-square-metre house can take a maximum of three days to assemble. The company says that if the owner prefers the house built on location, hence the need for foundation, the unit would then require 15 days to construct the base and allow time to cure, then three days to assemble the structure. In terms of cost, industry estimates put cost savings at 25-30 per cent.
Other techniques
Prefabricated or steel frames provide another option for potential homeowners in Kenya. They are available in attractive designs – walls can be done in fibreglass – and the finishing in each house can be tailor-made to suit individual tastes and budget.